Top 5 Common Problems in Plastic Sheet Welding and How to Solve Them
- Share
- Issue Time
- Jul 28,2025
Summary
Plastic sheet welding is widely used in industries like chemical storage, water treatment, and geomembrane projects. But issues such as warping, porosity, and misalignment can weaken weld quality. This article outlines the top five common problems and provides practical solutions to improve welding strength and efficiency. Weissenberg’s DVS2207-certified machines offer reliable support in solving these challenges.
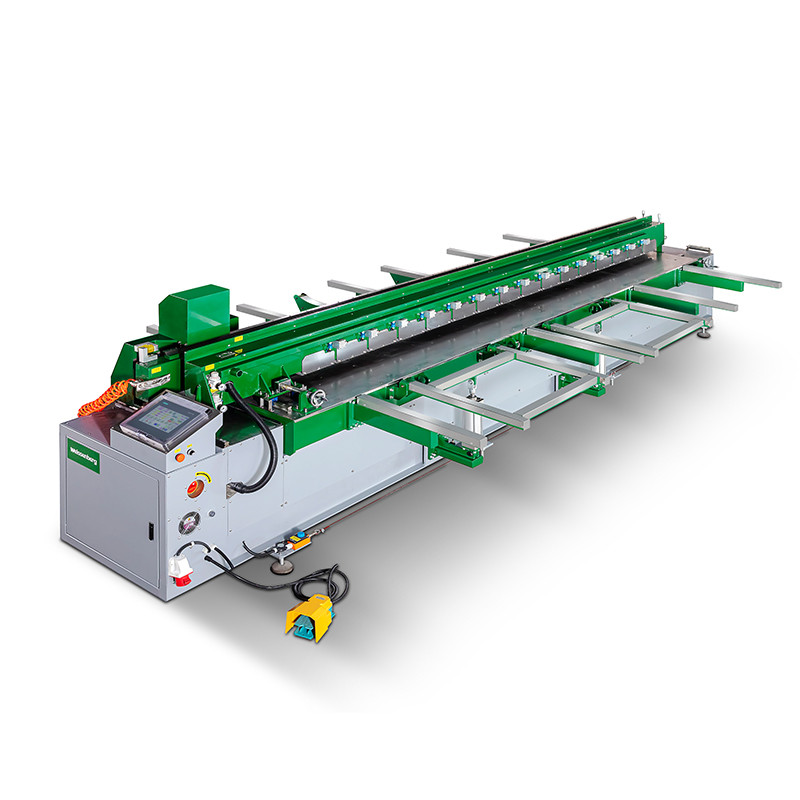
Meta Description: Explore the top 5 most common plastic sheet welding problems, including warping, porosity, and seam misalignment. Learn how to solve them with Weissenberg's DVS2207-compliant welding machines.
Plastic sheet welding is widely used in industries such as chemical storage, water treatment, geomembrane construction, and plastic tank fabrication. Common materials include HDPE, PP, and PVC. While welding may seem straightforward, challenges such as warping, voids, and misalignment often arise and compromise weld strength and integrity.
1. Heat Warping and Dimensional Instability
Plastic sheets may warp if heating is excessive or uneven—especially on large weld areas or with poor control.
✅ Solution:
- Use plastic sheet butt fusion machines with automatic temperature and time control (e.g., Weissenberg machines compliant with DVS2207, ≤ 5°C temperature variance).
- Apply synchronized clamping systems to keep sheets flat and aligned.
2. Porosity and Internal Voids
Porosity often results from surface moisture, contaminants, or overly rapid heating, leading to weak or leaky joints.
✅ Solution:
- Ensure sheet surfaces are dry and clean before welding.
- Use extrusion welders with consistent temperature and pressure (e.g., Weissenberg BOOSTER EX2 / EX3) for even bead deposition.
3. Weak Weld Strength or Cold Welding
Welds may appear fine but fail under stress due to incomplete internal fusion.
✅ Solution:
- Select the right nozzles and welding rods for your material (HDPE/PP/PVC) and adjust speed and heat settings accordingly.
- Use automated hot air seam welders (Weissenberg models offer programmable control for consistent heat and pressure).
4. Misalignment Due to Material Shrinkage
As HDPE and PP cool, they shrink, causing joints to shift and seams to misalign.
✅ Solution:
- Maintain clamping pressure until full cooling is achieved.
- Pre-calculate shrinkage ratios in design and leave an appropriate allowance.
5. Improper Edge Preparation
Dirty or rough edges reduce bonding efficiency and increase the risk of cold welds.
✅ Solution:
- Clean or trim the sheet edges using proper planers or scrapers.
- Weissenberg offers integrated edge preparation tools for clean pre-weld surfaces.
Why Choose Weissenberg?
- ✅ ISO 9001:2015 certified factory
- ✅ Full compliance with CE and DVS2207 welding standards
- ✅ Complete range of butt fusion welders, extrusion welders, hot air seam welders
- ✅ OEM / ODM options available to meet global market needs
👉 Explore our product range: www.weissenbergwelder.com
FAQ
- Q: What plastic materials can Weissenberg machines weld?
A: HDPE, PP, PVC, PVDF sheets and rods. - Q: How do I choose the right welding machine for my project?
A: Selection depends on sheet thickness, application (indoor/outdoor), and production needs. Contact us for guidance. - Q: Do you offer remote support or demos?
A: Yes, Weissenberg provides virtual training, remote commissioning, and live support for international customers.
Contact Weissenberg
🌐 Website: www.weissenbergwelder.com
📧 Email: inquiry@weissenbergwelder.com
📍 Address: Dongguan, Guangdong, China